Q&A: Supply Chain Planning & the Digital Supply Chain Network™
This is a question-and-answer session from the panel on The New Era of Supply Chain Planning: Planning Married to Execution.
Q: How are you managing data discrepancies across trade networks? And how long does it take to onboard a trade partner on One Network in cases where data is not normalized?
We run master data as a service with item cross referencing, so the data is always normalized from an item perspective. The discrepancies reveal themselves given that we build a logical value chain (as described in the webinar). Tthus any logical disconnects are identified and pushed to the dashboard/workbench. If the problem is a data issue rather than a demand/supply/logistics problem, it will be flagged and resolved. Because the network is a real-time, single version of the truth, these discrepancies are identified and resolved fairly quickly. This also gives us the advantage of not having to wait on a big data project to resolve for master data or transactional inconsistencies. We can solve those process-by-process, and over time a complete master data solution will have emerged as part of generating value rather than running an overhead data exercise.
Q: Does the adaptive system incorporate the inputs from open/public sources; i.e., in case of any supply chain disruption, what level of information does the system provide?
Yes, ONE is a network of networks and currently incorporates inputs from many sources, including public sources, for example telematics, including traffic and weather information.
Q: How are suppliers providing data for S&OP if they are not also on the One Network? Same questions for real time execution data from suppliers.
Typically, on the execution side they are delivering under contract and communicating through EDI, a portal, or some other mechanism. So, they are sharing execution data in some fashion, because an order is in motion and material is being processed. However, the collaboration around the data, the accuracy of the data, and the completeness of the data, is a different issue. The network will use what is provided and can extend the model by using data bots to represent entities in the network if they do not want to represent themselves.
Q: How are suppliers providing data for S&OP and real-life execution if they are not also on the One Network?
Most suppliers and carriers onboard because they see the value in an improved demand signal, and in improved collaboration around forecasts and orders. For those that don’t onboard, we can represent them on the network and use data bots to populate relevant information, as we have both master and transaction data, and history based on the existing contractual relationship.
Q: Are you able to show an example demo of what optimized execution actually looks like in your system?
Yes. While in action many of the processes run autonomously, for the demo we will show what is happening behind the scenes. For the interactive decision making through smart prescriptions, we demo both the workbench and the graphical interaction. Then with the dynamic flows, we show how these decisions carry across multiple roles and organizations in a single workflow until the opportunity or problem is completely addressed, all the way through to delivery/consumption.
Q: The planner role seems to change a lot as they will no longer be the “bridge builders” between planning and execution. What new skills will be needed tomorrow to get the best from optimized execution?
The job will be more interesting! Rather than firefighting and preparing reports, planners can focus on rules, policies, KPI’s and making decisions which will generate significant value for their enterprise, their partners, and especially their customers.
Q: What is the role of IoT on the shop floor, to pick up the trends in deviations between the plan and execution?
IoT is a data source for the network. The network itself is state based, and can follow state changes down to the millisecond. So, as raw material moves downstream changing state until it is finally consumed as an end product, the network has the ability to act on all data related to those state changes. That is why I mentioned it is so good at tracking ESG-related targets. So, for the shop floor, we would pick up the IoT data, similar to the way we take in data for cold chain variables like temperature deviation. Then, if a variable causes a problem, the system will either react autonomously, or with smart prescriptions interactively in the workbench. IoT data is also a big part of the MRO services.
Q: What is the average implementation lead time to get to a minimum viable solution?
Implementation time is typically 4 to 6 months. We usually target bigger value processes first so that subsequent “business releases” pay for themselves. Plus, we run a “tunable system of control” that interoperates with your current systems that provide value to the processes being improved. Alternatively, we can replace them during implementation, or at some point in the future.
Q: Has this solution been implemented in cases where the supply network is multi-layer-deep, especially when OEM only has a commercial relationship only with the Tier-1 supplier?
Yes, this happens frequently in today’s market. There are also hybrids where the upstream suppliers may be buying materials off the OEM’s contract or that the OEM has directed parts to the tier 1 from higher tier suppliers.
Q: If there is an issue projected 5-6 months out in the future, is there still a benefit to having the plan married to execution in real time?
Yes. The plan six months out, still has long lead time for material and capacity planning. If they are planning on the wrong mix or wrong volume, they are making bad decisions. When demand has shifted an hour out, or 6 months out, it is always better to make sure the team shares that in a near real-time, single version of the truth, so it can be acted on if necessary.
Q: How the platform deals with a make-to-order environment? Is there any manufacturing scheduling piece at the execution level?
The platform can be configured as an order-driven system, with replenishment and multi-echelon inventory optimization (MEIO). The network itself uses a distributed bill of materials upstream through all tiers of suppliers to raw material. For the manufacturing schedule we including manufacturing variables in the model in terms of the schedule, and for MES, sequencing, or other more detailed mechanism we typically partner or interoperate with the solution in place. Once the network is solving for issues around demand and supply variability our customers reduce the freeze schedules in manufacture to gain more resilience in the face of fluctuating demand and supply.
Q: You said the solution is “an architectural solution” to solving planning. How is that different to other planning solutions out there?
The platform uses a single data model for planning and execution, everybody is playing on the same field. This enables continuous and incremental planning, and thus continuously optimizes execution, even as demand, supply, and capacity shifts.
Watch Now: The New Era of Supply Chain Planning
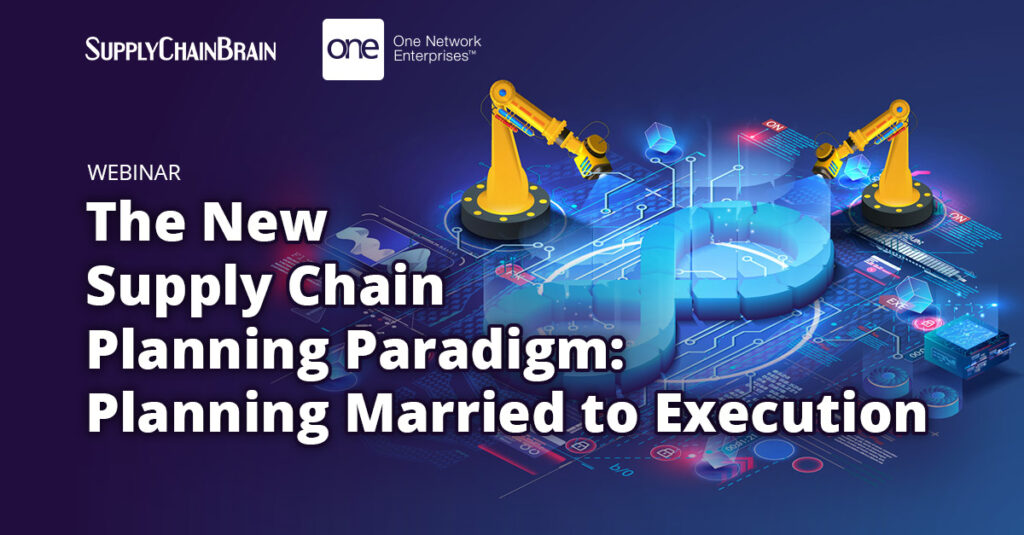